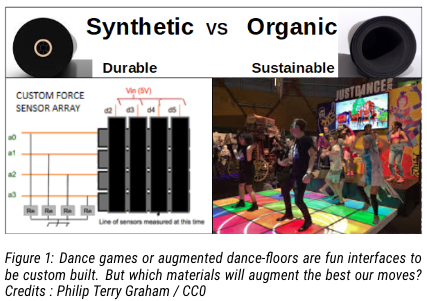
PapierLogik aims for using as much as possible a cellulose sustrate for the core assembly of their components.
These core assemblies are made of various electro-functionnal paper-based and printed layers.
Their design and content depend on the component to be produced. They are made of local, renewable and recycled resources and they are biodegradable and compostable.
Depending on the application, these functionnal cores are encapsulated with an unbounnded pure thrmoplastic layer, so that the whole can ultimately be delaminated and put in the recycling bin.
Such differences with fully plastic-based electronics represent huge imporovements in terms of electronics recycling and waste management.
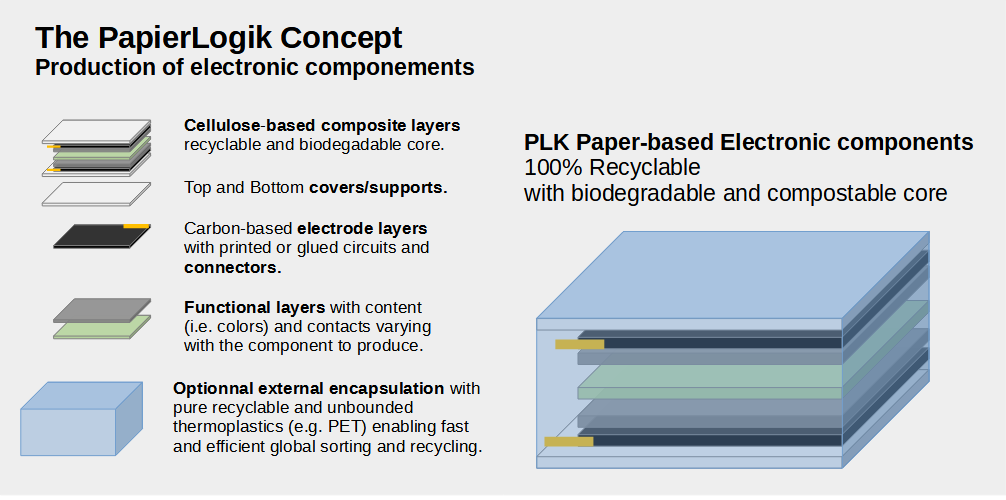
Paper-Based Resistive sensors
In the case of force sensing resistors and other touch or resistive based sensor, the sensor is built onto a resistive substrate acting as a piezoresistor and sandwinched between 2 electrode layers. When the 2 electrodes are connected, a current flow through the resistive layer and the resulting resistance of this component is function of the load or the force applied to compress the layers.
THe core substrate is our Volume Resistive 100K paper, and the electrodes layers are either the Volume Resistive 1k paper or else our bifunctionnal 100K/1K paper ascarbon printed layers printed onto one side of our Volume Resistive 100K.
Customizable sizes and shapes that will fit with your product design.
This enables the design and production of a variety of contact sensors among ohers, such as force, position, flexion and combos or arrays of such sensors designed as sensitive or control surfaces.
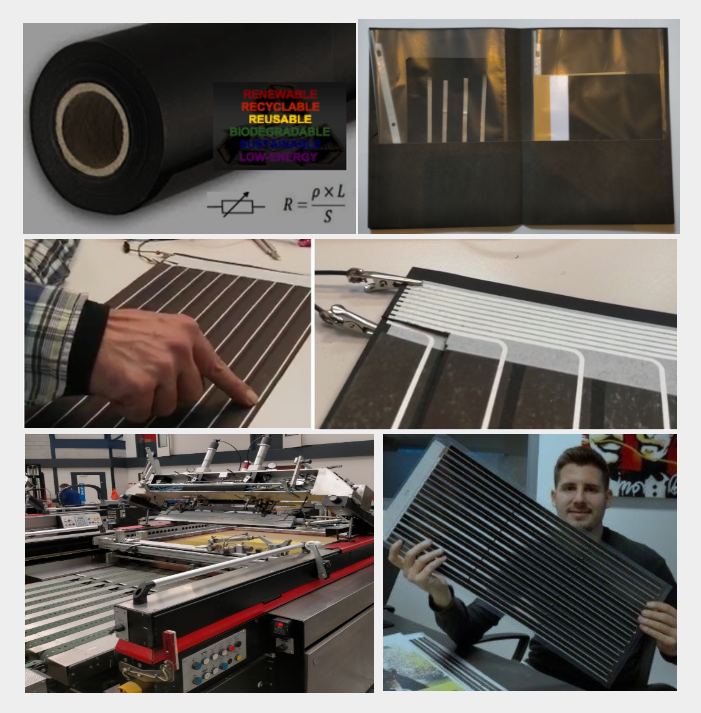
Responsive and repeatable signals vs position touch or force loading for fast production of detection, control or quantification interfaces.
Such sensors have a considerably low cost potential with relative precisions, making it valuable for a variety of applications that can be put into 3 main cathegories: detection, quantification and control.
PLK-Touch sensors are highly sensitive and responsive, with a high resistance variations for loads below 2kg/cm2, which makes of them excellent resources for real-time detection with home-aoutomation Floor and Walls Sensors, and control with Digital Music Instruments design.
They also provide a repeatble response and a relative precision of up to 3% of the load applied, with limited and manageable drift.
You can then have a flloor sensor responding to your steps for automatic lights control but filtering your animal by weight, or else you can design a musical touch pad sending sounds and aftertouch proportionnally to the force and sustain applied on the key.
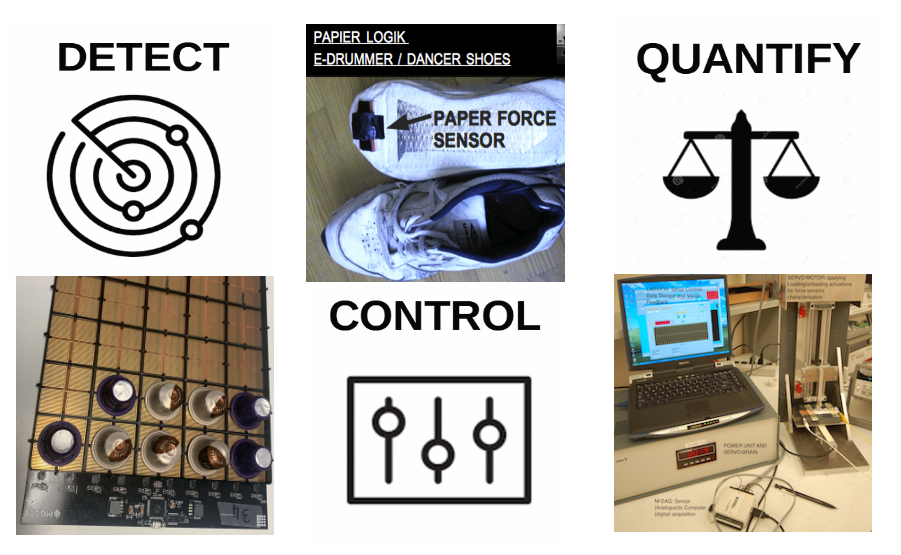
Application Examples
Digital Music Instruments
This long road of tested applications since 2005 started with Digital Music Instruments at IDMIL, MusicTech, McGill, with the goal for finding new ways for the fabrication of custom sensors that can be shaped and sized to the desired application, while providing high fidelity response for real-time applications.
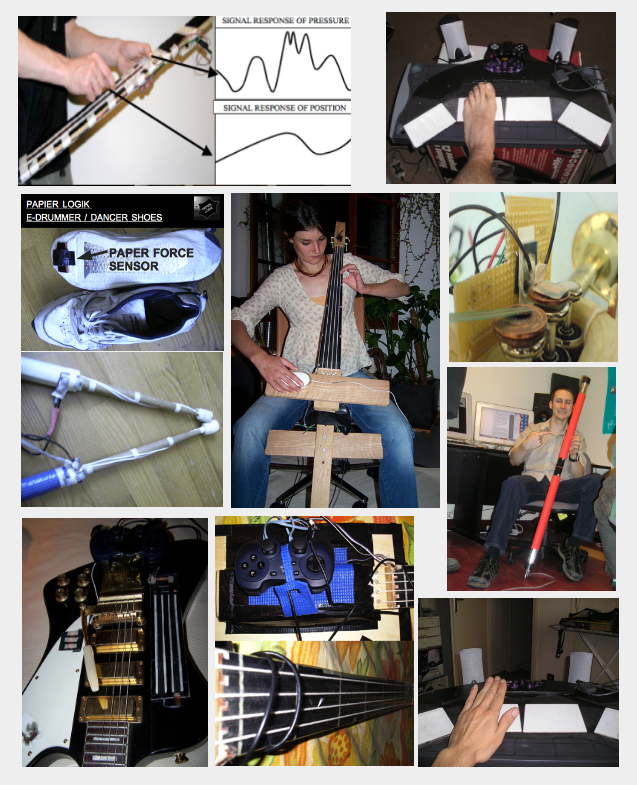
Whether this is about inpsired, augmented or alternate instruments, PLK-Resources and development tools let you design you own sizes and shapes of sensors to be used as parameters selectors or else as dynamic touch sensors for real-time sounds triggers and control.
This takes efficient materials, sensors and DSP to provide the most sensitive and responsive but efficient and "playable" Digital Music Instruments Design.
Computers-control peripherals
Based on our experience building DMIs, we were also able to explore ideas and tools for the production of exiting or alternate computer peripherals equipped with touch buttons and analog/position sensing such as keyboards, mouses, touchpads or else various gamepads and gaming controllers.
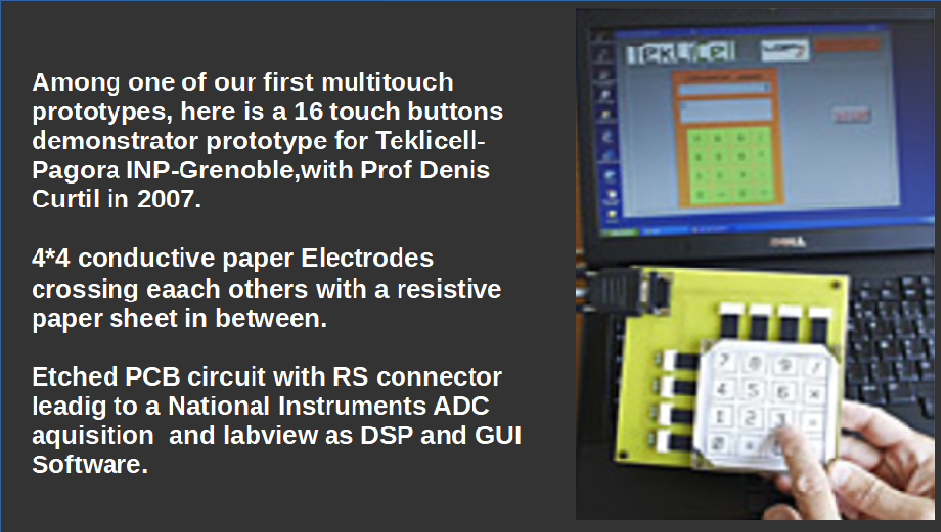
The reproductions of Keyboards and Controller arrays through fast analog multiplexing of force paper sensor arrays design, enabling to build a fully customizable multi-touch controller that can for instance complete your keyboard wwith shortcuts, sound triggering, etc...
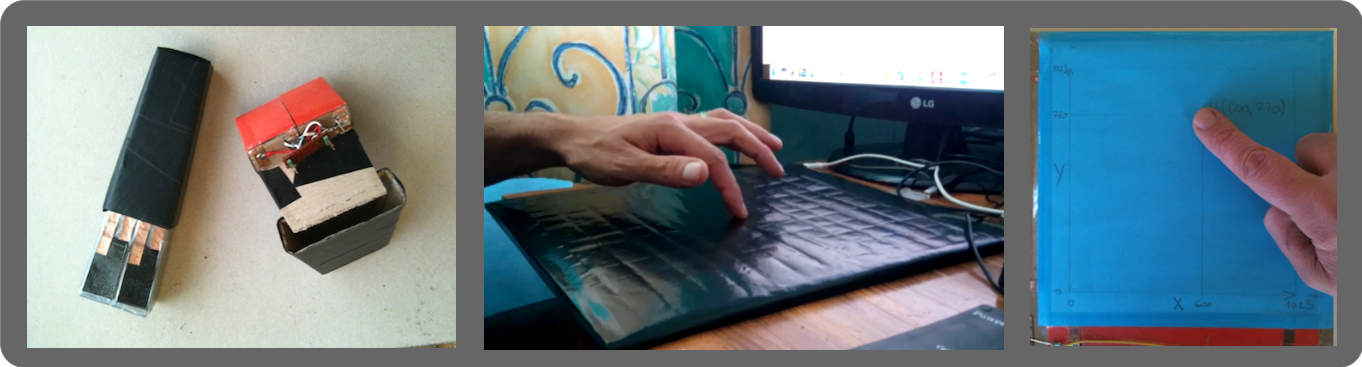
Video Game Controllers
Specific interfaces developped to be plugged onto modified PS GamePads could thus be design to provide more immersive gamplay.
Large floor sensors can be used as dance floors or to trigger your avatar's movements, while other sensors can be used as eevent, selection or action buttons and even combos in the case of an interface for Tekken, and disposed onto your immersive environment, interface or objects like music intruments for Rockband of course.
Control Pannel
Control pannels always need command button to trigger or adjust an electric signal than can then directly control or else send data to any electrical or electronic device you can plug to.
Once you are able to understand how you can act onto a system or how its controls act onto it, You can then reproduce these control pannels in paper, or else create original improvements.
As an exampe, if you can replace the button of an automatic Doorbell with custom paper sensors, you can then build and set a large floor sensor underneath your door carpet and turn it into an automatic doorbell trigger that will surely surprise your visotors.
Home-Automation
Home automation is not only about light and temperature controls from floors and walls, but it can also involve your
furntirture such as in the case or this originally E-Jumbe built on a wooden industrial wires rack and ultimately turned as an interactive living-room table that does not only enables to play MIDI drums, but it can now also be used to interact with the wifi station for light control and other media controllers.
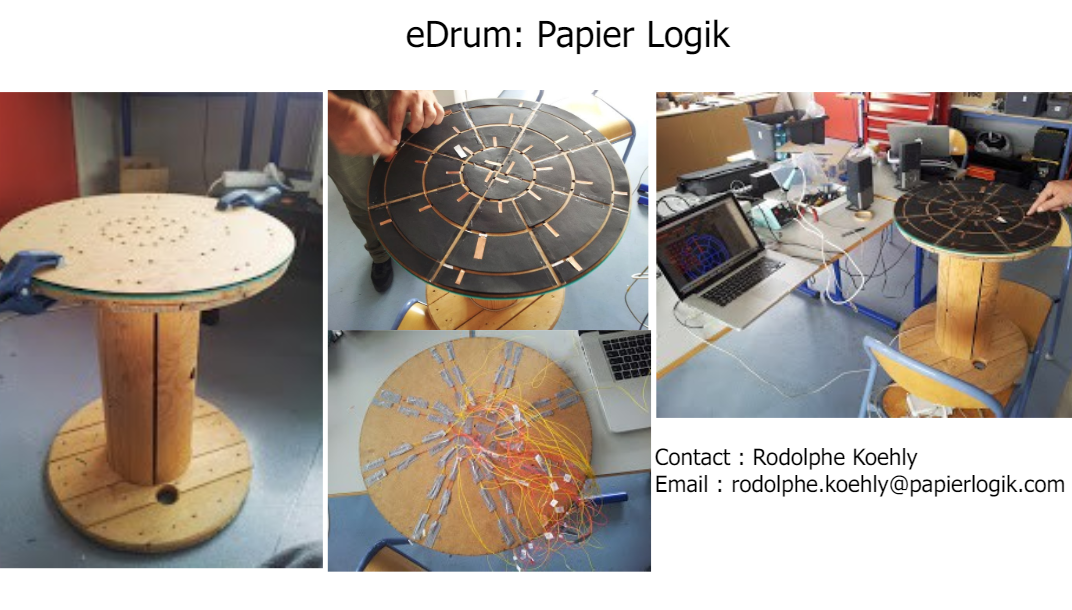
Immersive spaces
Large spaces of floors and walls or furniture can be coverd by PLK papers and turned into active controllers to produce a variety of interactive games, video games or more generally presence detection controls.
The application example below proposed by the artist and researcher Marije Baalman for an interactive multimedia performance and game interface called Treasure Islands, to use large floor sensitive areas underneath a tapestry controlling in this case projected visual feedback and sounds based on the user moves.
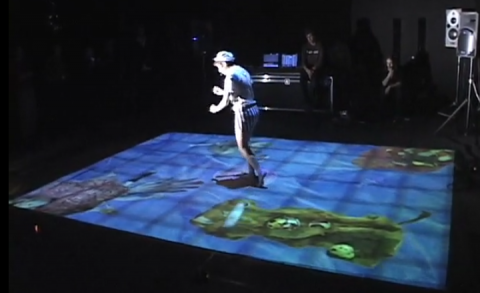
HealthCare
Various prototypes have been developped since 2010 for podometry, bio-sensors, muscular and compression force measurements, physiology and even dentistry tools and Anatomy evaluation of Horse muscles
Sports and gaming Interfaces
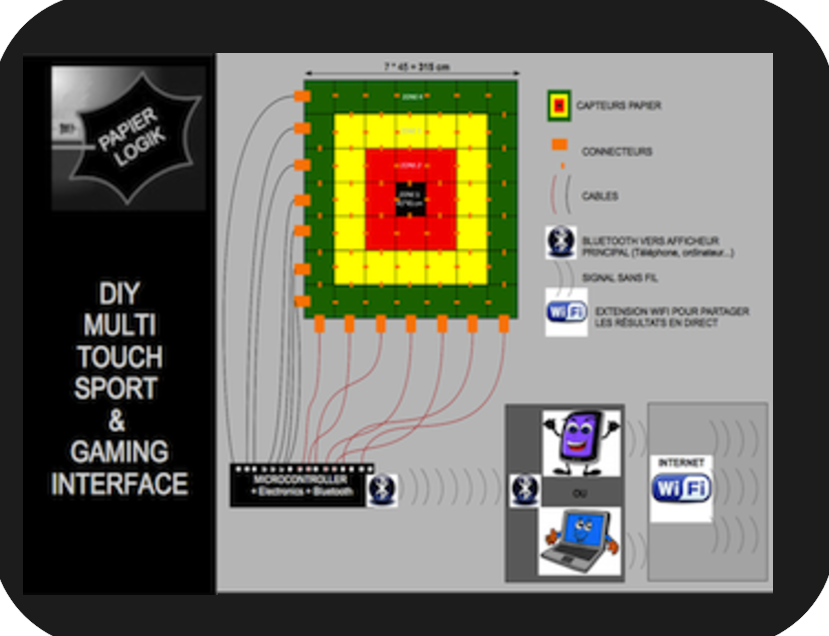
Arena of Destiny (2016-2024)
We experienced 4 POC, prototypes and demonstrators of a tactile body armor detecting contact,force and hits applied onto 14 areas of custom paper force sensors wrapped into vynile and textiles, and driving 6 sgnals towards theinteractive cloud and game AI of Arena of Destiny using ESP32-based communication interface and hardware driver;
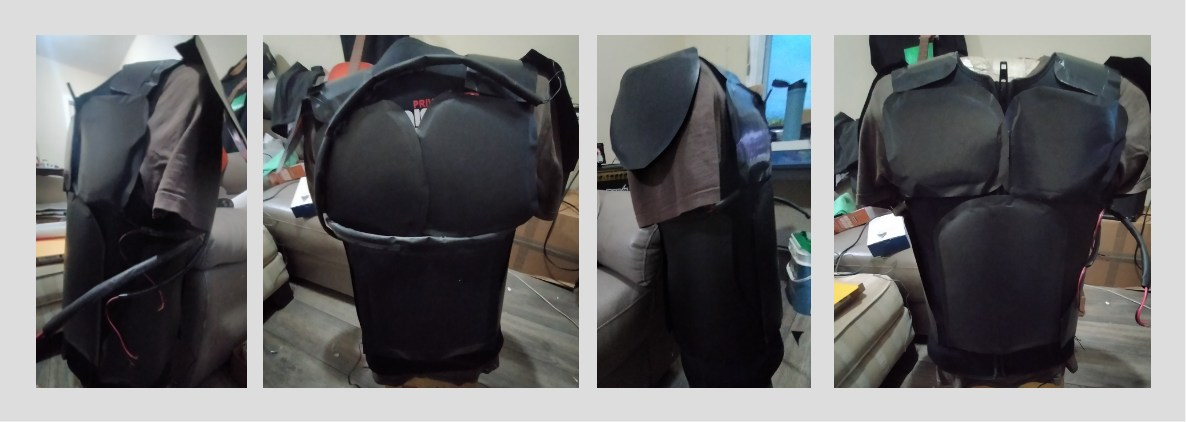
Extreme Wash (2012(
A paper-based force sensor designed into a waterproof matress to evaluate the required forces for handwashing tissues with P&G microballs laundry products.
Paper Combustion (2007)
Paper burns faster and better than plastics due to its high porosity. Carbon-loaded paper were ued to build a one time performance using a large connected sheet and burning it. The ashes would remain conductive until falling or being remove by the user, thus increasing the connected paper resistance, while an automated program would exploit these variations to generate sounds variations.